Stepper motors offers many attractive features such as:
• Available resolutions ranging from several steps up to 400 steps (or higher)
per revolution.
• Several horsepower ratings.
• Ability to track signals as fast as 1200 pulses per second.
APPLICATIONS:
Stepper motors have many industrial applications such as:
• Printers.
• Disk Drives.
• Machine Tools.
• Robotics.
• Tape Drives
TYPES:
Stepper motors are usually classified into three main categories, namely,
1) Variable reluctance (single stack and multi stack),
2) Permanent Magnet, and
3) Hybrid motors.
Single Stack Variable Reluctance Stepper Motors:
The stator is made of a single stack of steel laminations with the phase windings wound around the stator poles. The rotor is made of stack of steel laminations without any windings. The main principle of operation depends on aligning
one set only of stator and rotor poles by energizing the stator windings. Therefore, the number of poles in the stator and rotor windings has to be different. The stator windings are energized by a DC source in such a sequence to generate a resultant rotating air-gap field around the rotor in steps. The rotor is made of ferromagnetic material that provides a tendency to align the rotor axis along the direction of the resultant air-gap field. Therefore,the rotor tracks the motion of this stepped field.
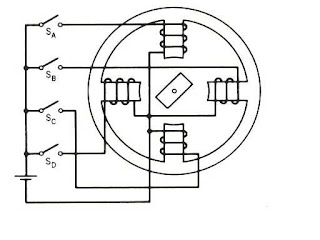
Basic circuit configuration of a typical 4-phase, 2-pole,
single-stack, variable reluctance stepper motor
Multi-Stack Variable Reluctance Stepper Motors:
In this type, the motor is divided along its axis into a number of stacks. Each stack is energized by a separate winding (phase).These stacks are magnetically isolated from each other. The most common type is the three-stack, three-phase motors;however, number of stacks and phases up to seven are also available.

The direction of rotation can be reversed by reversing the switching sequence. Assume that the total number of stacks (phases) is N while the total number of teeth in each stack is x.
The tooth pitch ( ) τp can be expressed by,
τp =360/x
Moreover, the step size (Δθ) can be expressed by,
(Δθ)= 360/xN
Consequently, the number of steps per revolution (n) is given by
n = (360/(Δθ))= xN
Permanent Magnet Stepper Motors:
Permanent magnet (PM) stepper motors are similar in construction to that of single-stack;variable reluctance stepper motors except that the rotor is made of permanent magnet.PM stepper motors offer many features compared to variable reluctance type such as
• Higher inertia and consequently lower acceleration (deceleration) rates.
• Maximum step pulse rate is 300 pulses per second compared to 1200 pulses per
second for variable reluctance stepper motors.
• Larger step sizes, ranging from 30° to 90° compared to step sizes as low as 1.8° for variable reluctance stepper motors.
• Generate higher torque per ampere of stator currents than variable reluctance
stepper motors.

Construction and operation of 2-phase, permanent magnet stepper motor
Hybrid Stepper Motors:
Hybrid stepper motors have similar stators’ construction to that of variable reluctance stepper motors. However, their rotors constructions combine both variable reluctance and permanent magnet constructions. The rotors are made of an axial permanent magnet at the middle and two identical stacks of soft iron poles at the outer ends attached to the north and south poles of the permanent magnet. The rotor poles connected to the north pole of the permanent magnet forms North Pole, while the other forms the south poles.

Cross section view of 4-pole stator and 5-pole rotor hybrid stepper motor
Modes of operation:
1. Start-stop mode
2. Slewing mode
No comments:
Post a Comment